Eliminating moisture from the PCB is essential for any PCB manufacturer. This can be achieved by baking the PCBs. If the moisture is not removed properly, then it may lead to the dysfunction of the board while implementing it in the device. But, before moving further with this topic, let us first learn what is typically meant by “bake-out”? “Bake-out” is a process of removing volatile compounds from materials, using high-temperature (100 to 125°C) or vacuum, before placing the material in an environment, where the slow release of these volatile compounds would hamper the performance of a device in which these materials are used.
The bake-out process in PCB, by its name, refers to baking the PCB at a temperature of 100°C (or more – if required), following the guidelines described under IPC 1601, to eliminate outgassing of moisture from the copper plating in plated through holes (PTHs). This occurs during manual or automated soldering processes that cause pin-holes, blow-holes, and sunken solder-fillets. The process of baking should be done in a clean oven in order to prevent the PCB from any kind of contamination that can occur during the process. It is also recommended to place the boards in such a way that the air can circulate freely around them during the baking process. Since we want the moisture (and other solvents, possibly) to escape, the best way to do this is to have the PCBs in a rack, vertically oriented with some space in between them. If the boards are stacked on top of one another or flat on the base of the oven, etc., then it can be more difficult for the moisture to escape. Overall, it is highly advisable to prevent moisture from reaching the PCB which can be done via pre-baking.
How we bake PCBs at WORLD electronics
Approach: Our team determined baking the printed circuit boards at receiving, prior to assembly for a minimum of 4 hours at 125°C and a maximum of 16 hours would meet IPC-1601 standards (Printed Board Handling and Storage Guidelines). Moisture barrier bags in a range of sizes were ordered for storage of the circuit boards after completing the PCB baking process. Two system programs were created within our existing production software for levels of baking PCBs (low temp and high temp).
Results: Our standardized printed circuit board bake-out process has dramatically decreased production time and minimized PCB fall out which results in fewer problems, quicker QC inspections, and higher quality circuit boards without fear of latent failures.
Why PCBs are Baked?
- To remove moisture from the PCB for delamination/outgassing prevention
- To increase the life-span of the board
- To improve the performance of the PCB used in the intended device
Moisture could lead to various functional failures on a PCB. It can fester in the epoxy glass and leads to cracks in the board. It is also responsible for causing separation in the PCB layers, especially interfaces. The presence of the moisture could slow down the circuit speed and can increase the delay time. If such problems exceed up to a certain limit, the device might simply fail to work. The next reason for baking PCBs is to inhibit the delamination of boards that occur during soldering. It happens when moisture accumulates in voids or at the interface between the epoxy/laminate on poorly bonded multi-layer boards. During soldering, the moisture turns into steam/water vapor and expands which creates pressure that can cause the device to fail. Hence, one can say that the most common cause of delamination is moisture, and pre-baking the board before soldering will reduce the cause of it. The chronological order would be to first bake the PCB and then do soldering if you want your PCB to function properly.
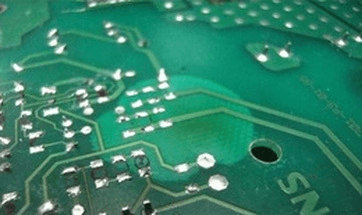
The picture given above shows a similar example of an FR4-based PCB’s delamination during reflow soldering. It happens due to the moisture present within the FR4 material that expands causing internal layers to separate. The FR4 is a “hygroscopic” material that absorbs moisture from the atmosphere. Hence, once the PCBs are fabricated, they should be vacuum-sealed. Therefore, predominantly, PCBs are baked to remove moisture. Although, PCBs constructed from Epoxy Resin are not so hygroscopic and hence there’s no need for baking. However, if the boards are old, or whenever there is a suspect of moisture in the boards, it is recommended to bake before soldering.
PCB bake-out in a nutshell
Parameter | Explanation |
Baking | To get rid of moisture |
Benefits | To improve functionality/to increase life-span of PCB |
Baking Temperature | 100-125°C |
Disadvantage | Higher production cost and time |
At WORLD electronics, we offer pre-baked PCBs to suit all your requirements which will deliver outstanding performance for the intended application.
Related Articles
Burn-in and temperature Cycling